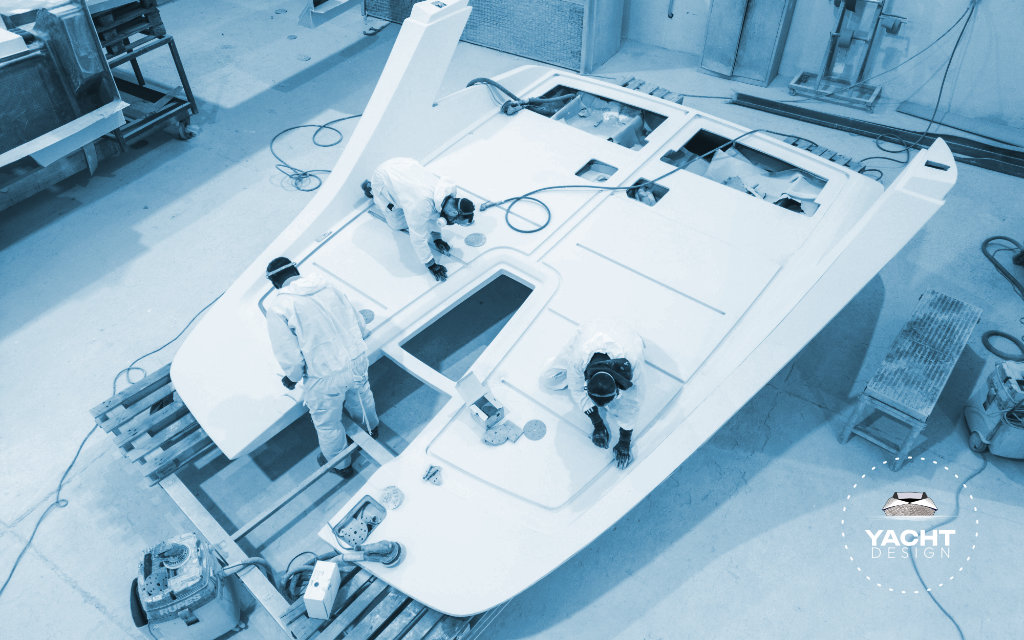
PROCESAMIENTO POST-EXTRACCIÓN
Una vez completado el proceso de fibra de vidrio, se infunden las piezas y se limpian los moldes de los materiales de consumo utilizados, para luego proceder al desmoldeado de las piezas fabricadas. Los moldes se construyen con segmentaciones (bridas atornilladas) para permitir la extracción de la pieza moldeada en caso de que haya geometrías que impidan su liberación (superficies con socavados).
El producto terminado presenta superficies brillantes, iguales a la superficie del molde en el que fue fabricado. Si el molde está en buenas condiciones y bien pulido, la pieza moldeada solo necesitará ajustes en las uniones de los moldes.
Durante el proceso de fibra de vidrio, y en particular durante la infusión, el calentamiento de la resina debido a la catálisis puede generar marcas de contracción. Estas son marcas o líneas visibles en las superficies brillantes del producto, especialmente en zonas donde la resina se acumula, generalmente en bordes afilados (estructuras internas, discontinuidades en el núcleo, mamparos, etc.).
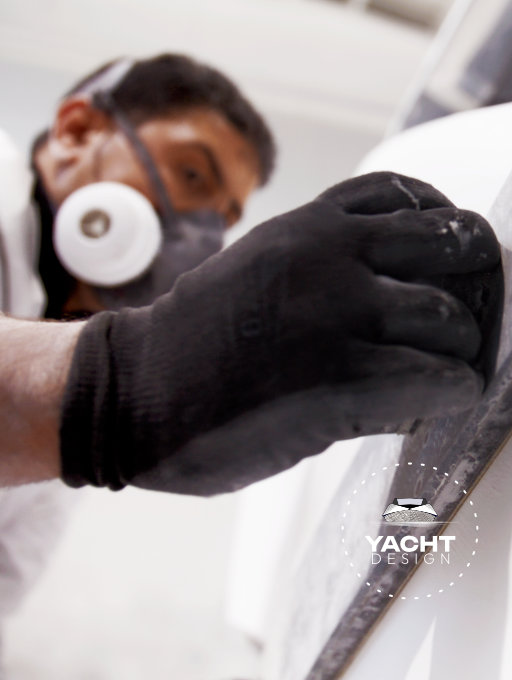
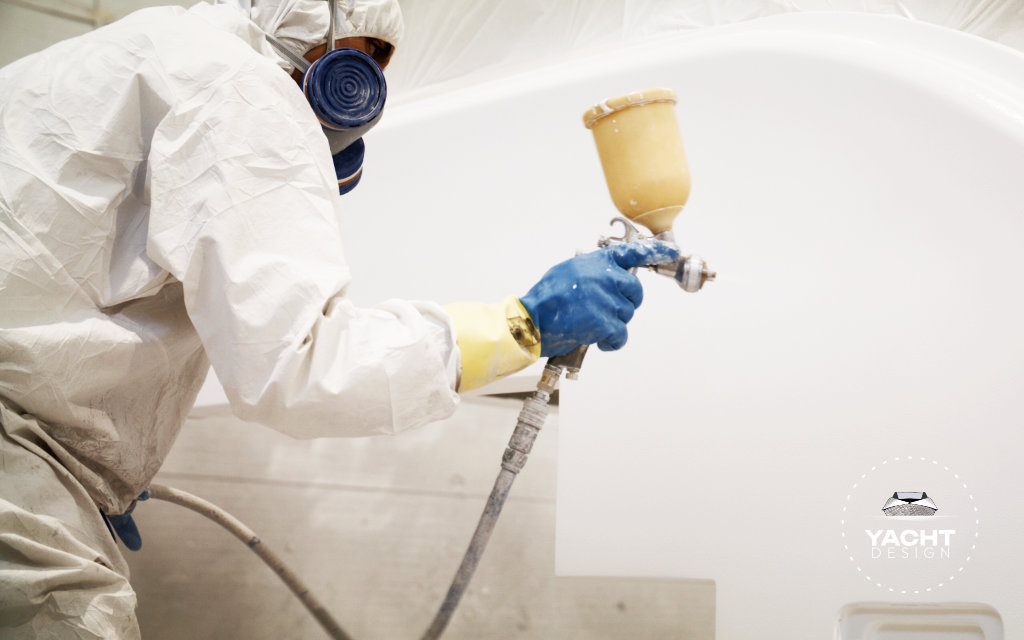
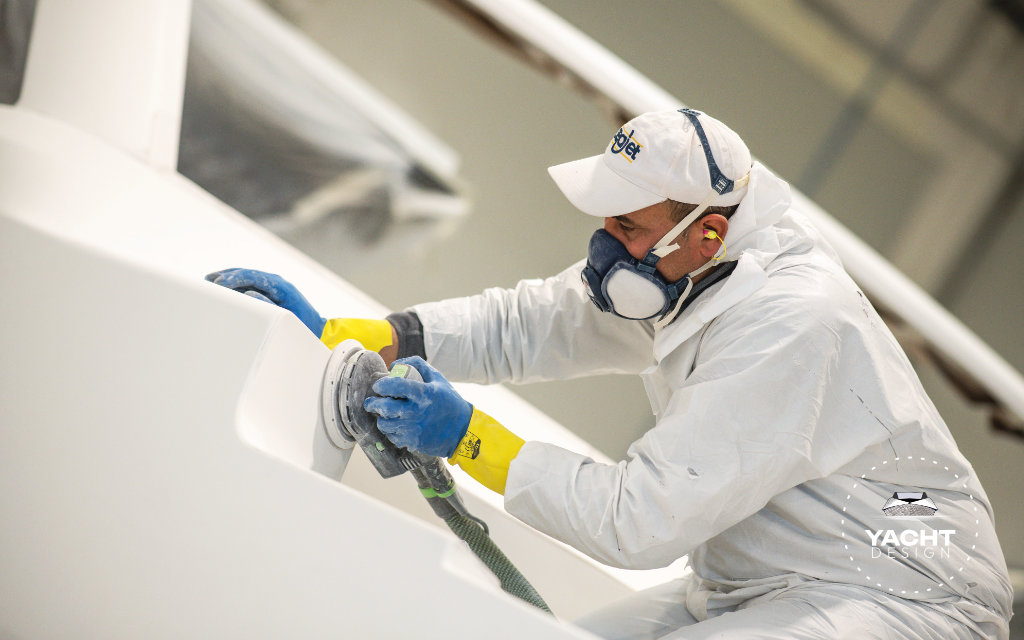
El primer proceso después del desmoldeado se llama recorte, que consiste en cortar y refinar todas las superficies formadas en el molde pero que no son necesarias en el producto final. En el sector náutico, esto incluye ventanas y ojos de buey que en el molde están cerrados, pero en la pieza final deben abrirse para el ensamblaje. Al mismo tiempo, si es necesario, se preparan áreas rebajadas raspando la resina para permitir la unión externa del componente.
Esta unión se realiza en fibra de vidrio cuando el producto se fabrica en varios moldes y luego se ensambla. Por ejemplo, una puerta con una función estética en todas sus partes se fabricará en dos moldes y luego se ensamblará. En el perímetro exterior de la unión se aplicará la faja de refuerzo.
CARROCERÍA PRELIMINAR
El acabado superficial de los productos de fibra de vidrio generalmente debe ser brillante y uniforme, sin irregularidades.
Para lograrlo, se realizan varias fases de lijado para eliminar defectos e imperfecciones de procesos anteriores. La primera inspección busca burbujas de aire que pueden formarse en la capa superficial o entre las capas del material.
Estos defectos ocurren por una laminación manual deficiente o por una presión insuficiente sobre los materiales estructurales. Si no se eliminan, las burbujas pueden causar defectos estéticos o grietas con el tiempo, ya que se expanden con el calor.
La reparación consiste en abrir las burbujas y lijar la superficie. Si son pequeñas, se rellenan con masilla de resina reforzada. Si son grandes, se laminan con tejido hasta que se corrige el defecto.
El proceso de carrocería se realiza lijando con papeles de grano cada vez más fino para eliminar rayas y marcas. Se puede hacer manualmente con tacos de lijado o con lijadoras orbitales. Estas últimas son más fáciles de usar, pero dan un acabado inferior en comparación con el lijado manual realizado por personal capacitado.
El lijado comienza con papel de lija P40 en las uniones y áreas reparadas. Luego se usan:
- P80
- P120
- P220
- P400
Para detectar defectos en la superficie, se aplica un polvo negro o una solución alcohólica con polvo negro («guía de lijado»). Las zonas bajas o depresiones quedan visibles hasta que se eliminan por completo, momento en el cual se pasa al siguiente grano.