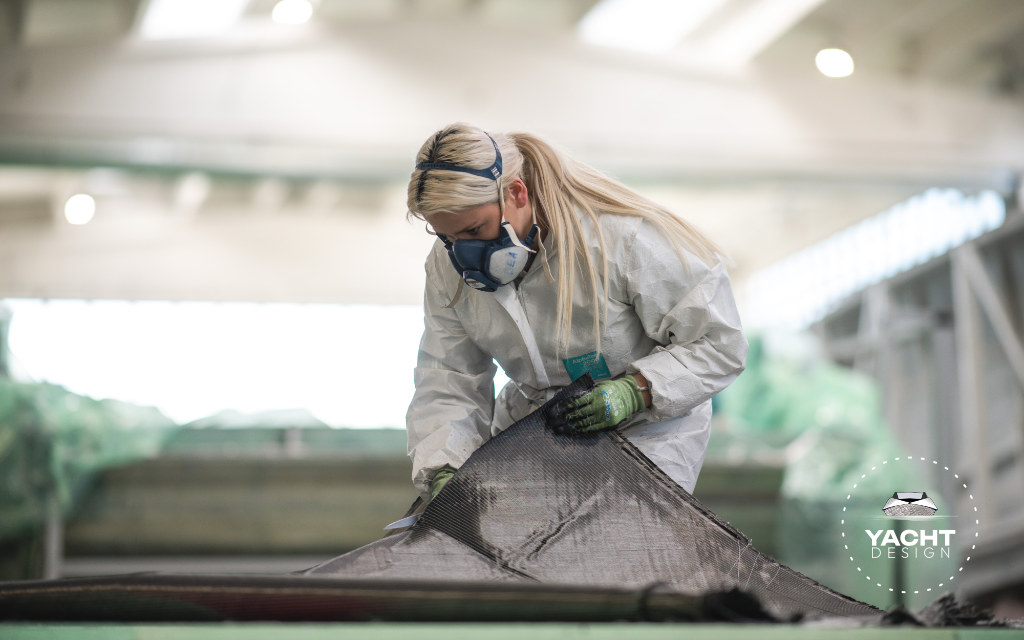
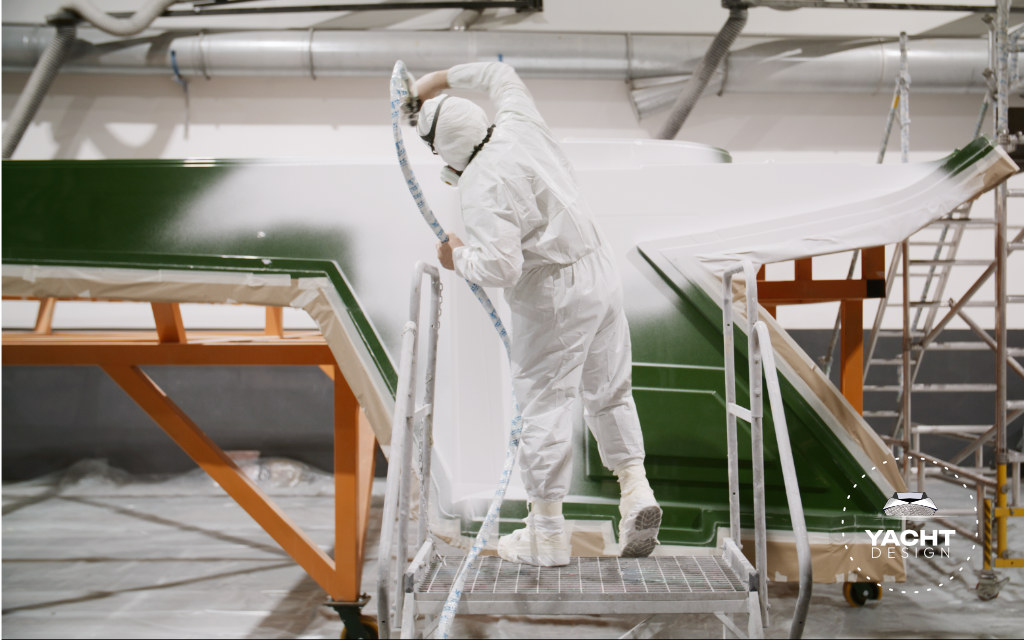
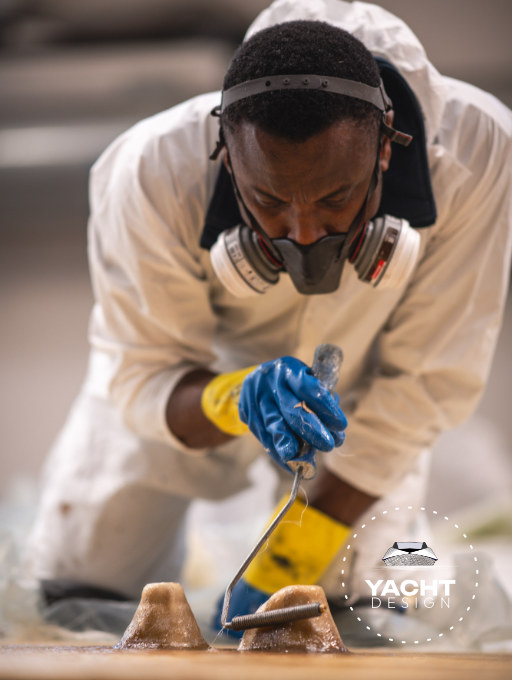
METODI REALIZZATIVI E PROCESSI PRODUTTIVI
I metodi realizzativi sono molteplici e con caratteristiche differenti, ma possono essere suddivisi fondamentalmente in due macro-gruppi: processi a stampo aperto e processi a stampo chiuso.
I processi produttivi dei materiali compositi sono molteplici, tra i più diffusi si ricordano:
· stesura manuale (hand lay-up / spray lay-up)
· stampaggio ad iniezione o compressione (injection o compression molding)
· formatura in autoclave
· stampaggio per trasferimento di resina (laminazione o bag molding / vacuum infusion / resin transfer molding RTM)
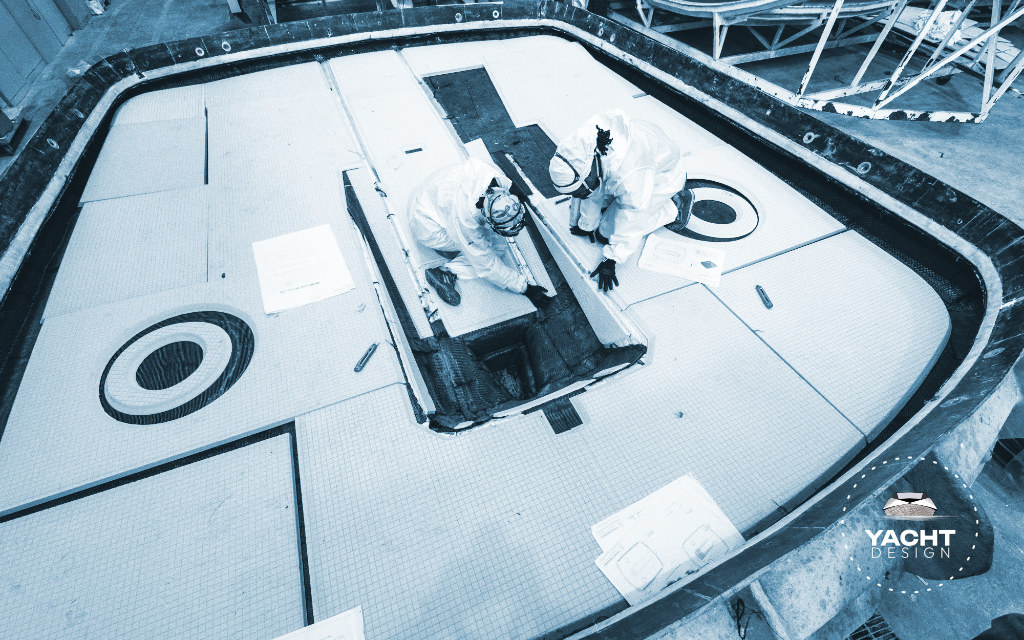
PROCESSI A STAMPO APERTO
I processi a stampo aperto sono metodologie di costruzione manuali e artigianali, tra i più antichi e semplici per la realizzazione di materiali plastici rinforzati. Vengono tutt’ora utilizzati principalmente per la produzione di particolari di dimensioni notevoli, che non richiedano elevati livelli produttivi, come ad esempio scafi di barche in vetroresina.
L’hand lay-up (Figura 17) è la tecnica più antica e prevede la deposizione manuale della fibra e della resina all’interno di uno stampo; successivamente si eliminano le bolle d’aria passando con opportuni rulli sopra il materiale; si ripete il processo fino al raggiungimento dello spessore prestabilito.
Un’evoluzione di questa tecnica è lo spray lay-up (Figura 18) nel quale al posto di depositare manualmente il rinforzo, lo si spruzza mescolato alla resina per mezzo di una pistola ad aria compressa. È un processo molto più veloce rispetto ad una deposizione manuale, però non permette l’utilizzo di rinforzi vetrosi, infatti la pistola spara la fibra tagliata in piccoli segmenti prendendola da delle bobine. In ambedue i processi si possono utilizzare stampi sia maschi che femmine, a seconda che il lato che necessita una migliore definizione sia rispettivamente quello interno o quello esterno, inoltre spesso si spruzza lo stampo con una sostanza, il gel-coat, che va a costituire lo strato esterno del pezzo finito.
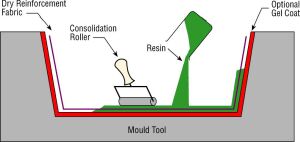
Figura 9 – Processo hand lay-up
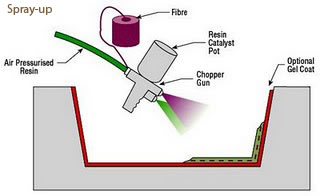
Figura 10 – Processo spray lay-up
PROCESSI A STAMPO CHIUSO
Le metodologie di formatura più classiche sono l’injection molding, una miscela di resina e carica viene iniettata in uno stampo chiuso, e il compression molding, nel quale la miscela è pressata dal controstampo all’interno del maschio.
La reticolazione delle resine è generalmente aiutata dalla temperatura alla quale vengono portati gli stampi, per ridurre i tempi di processo ed aumentare la produttività.
Spesso i rinforzi utilizzati sono costituiti da fibre corte o particelle che non vanno a creare una struttura resistente come un tessuto, non garantendo la continuità della fibra all’interno del pezzo finito.
Per ottenere laminati con caratteristiche migliori, oltre ad utilizzare rinforzi adeguati, si impiega il processo di formatura in autoclave, evoluzione della tecnologia con sacco a vuoto, in cui la pressione di compattazione del laminato è di parecchie volte superiore alla pressione atmosferica.
Il ciclo di polimerizzazione (tempo-temperatura-pressione) dipende dal tipo di resina, forma e dimensioni del particolare, materiale e spessore dello stampo.
Tra i vantaggi conseguibili si ricordano la bassa porosità del laminato, l’ottima finitura superficiale sulla faccia verso lo stampo, lo spessore costante del laminato, la grande ripetitività del processo grazie agli stampi metallici ed alla uniforme distribuzione di calore e pressione del ciclo computerizzato.
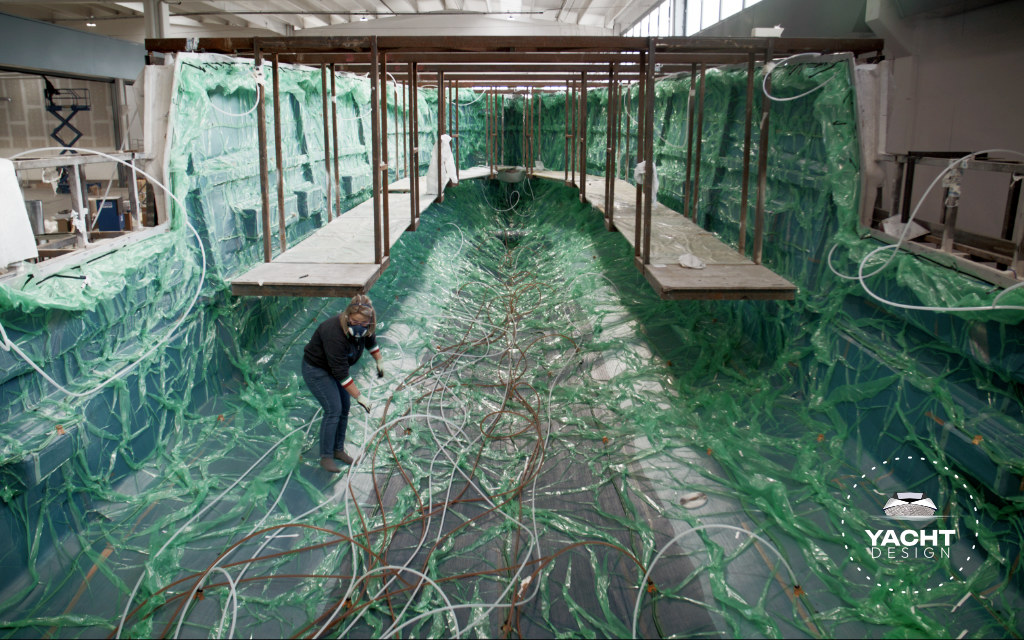
BAG MOLDING – INFUSION
È il processo di stampaggio in sacco per trasferimento di resina per effetto del vuoto. Si utilizza uno stampo maschio all’interno del quale vengono predisposte e stratificate le fibre ordinate, successivamente si chiude lo stampo mediante un sacco che serve per mantenere il vuoto, si dispongono dei canali per aspirare la resina miscelata con l’indurente da un contenitore e dall’altro lato dello stampo dei canali per tirare il vuoto, mediante un’apposita pompa. La sola pressione atmosferica permette la compattazione del laminato.
Una volta che il particolare è solidificato e la resina è completamente reticolata, si estrae l’oggetto, facilitandone il distacco dallo stampo facendo fluire aria tra le due parti, mediante opportuna valvola al di sotto del mandrino.
Gli stampi possono essere fatti sia in materiale plastico che in leghe metalliche, a seconda che l’intero processo avvenga a temperatura ambiente oppure a temperature maggiori per aiutare la reticolazione.
Il processo di bag molding (Figura 19) è utilizzabile sia per la lavorazione di oggetti di grandi dimensioni che aventi geometrie complesse.
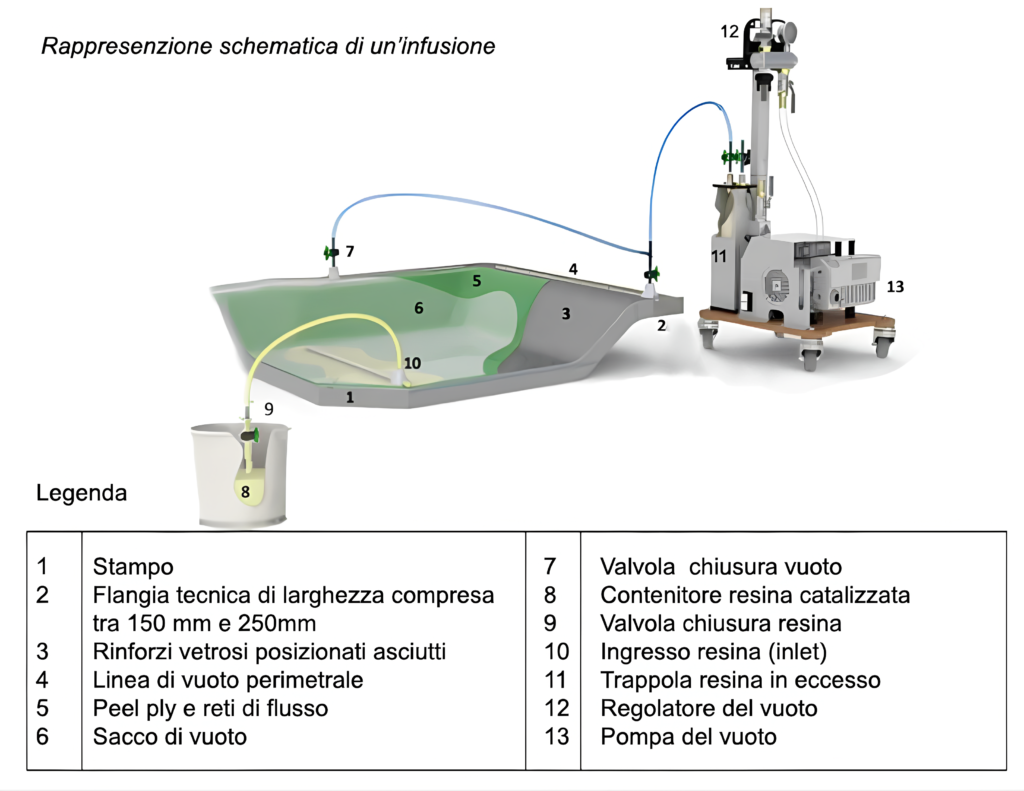
Figura 11 – Schema del processo bag molding
RESIN TRANSFER MOLDING – RTM
È un’evoluzione del processo bag molding nel quale, al posto del sacco per il vuoto, si utilizza un controstampo che viene chiuso sullo stampo per dare la forma definitiva all’oggetto. Il processo RTM classico non prevede l’utilizzo di pompe a vuoto, ma solo di una che porti la resina dal contenitore all’interno dello stampo.
La variante VARTM (Vacuum Assisted RTM) (Figure 20 e 21) prevede che la resina venga inserita al centro dello stampo e venga tirata, grazie al vuoto, verso la periferia dello stampo. Rispetto alle metodologie di iniezione e compressione, si ha il vantaggio di avere una migliore rifinitura superficiale su ambo i lati, mantenendo dei cicli di produzione veloci, riducendo inoltre la possibilità di trovare delle bolle d’aria all’interno della matrice.
Anche in questo caso gli stampi possono essere di diversi materiali, a seconda del tipo di polimerizzazione che è necessario eseguire. Vengono trattati con un distaccante per favorire il distacco dell’oggetto una volta finite le lavorazioni; successivamente si procede posizionando il rinforzo all’interno dello stampo e chiudendolo con il controstampo. La resina viene aspirata attraverso valvole, che vengono chiuse una volta che questa ha raggiunto tutti i punti dello stampo.
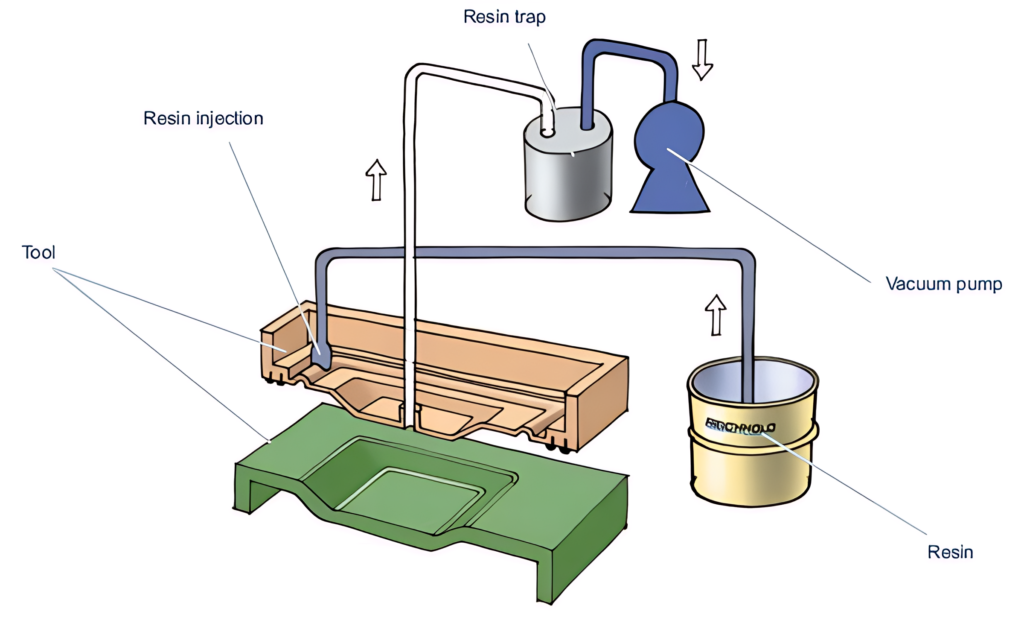
Figura 12 – Schema del processo VARTM
INFUSIONE
Una volta che tutti i materiali e i rinforzi sono stati correttamente posizionati, come da scheda di laminazione, si prepara il manufatto per l’infusione.
Per favorire lo scorrimento della resina liquida all’interno del sacco a vuoto, si devono predisporre dei canali (spiralina) ed una rete in materiale plastico. La rete viene fissata con la colla spray sulle zone monolitiche e non dove è presente il core, in quanto quest’ultimo è solitamente realizzato con scanalature e fori che servono per favorire lo scorrimento della resina e la corretta impregnazione di tutti i tessuti.
Il posizionamento della spiralina, delle aspirazioni del vuoto e degli ingressi della resina, sono il punto cruciale di tutto il processo, in quanto se non si bagnano completamente i tessuti, il manufatto non risulterà completamente rigido e strutturato (nei casi peggiori può non essere riparabile).
Esistono programmi di simulazione che permettono di modellare lo scorrimento della resina all’interno dello stampo, ma sono molto costosi e difficili da utilizzare, pertanto spesso si ricorre all’esperienza degli operatori e alle prove sul campo.